Cost Reduction Strategies in Manufacturing - An Overview
- Sukanya Chatterjee
- Jun 29, 2024
- 4 min read
Updated: Jul 2, 2024
Executive Summary
This article provides an outline guide for manufacturing directors, operations managers, and business leaders aiming to reduce costs in their manufacturing operations.
It summarises practical approaches, risks, and implementation challenges for each strategy, ensuring a well-rounded understanding of the process.
The goal is to help companies achieve sustainable cost reductions while maintaining quality and competitiveness.
This article offers a structured approach to cost reduction, emphasizing the importance of thorough planning, careful implementation, and ongoing monitoring. Each strategy is broken down into three key aspects: the approach, the associated risks, and the implementation challenges.
This structure ensures that readers understand the strategies and how to effectively apply them in their organizations.

Introduction to Cost Reduction
In the highly competitive world of manufacturing, reducing costs is not just an option—it's a necessity.
As margins shrink and global competition increases, companies must find innovative ways to streamline operations, enhance efficiency, and cut unnecessary expenses.
This article is designed for manufacturing directors, operations managers, and business leaders looking to make informed decisions about cost reduction strategies. By understanding and addressing the potential risks and implementation challenges, organizations can navigate the complexities of cost management and emerge more resilient and competitive.
Cost reduction is not merely about slashing budgets; it’s about making smart, strategic decisions that enhance overall efficiency and productivity.
Identify Waste and Streamline Operations
Approach
Utilize Lean Manufacturing and Six Sigma methodologies to identify and eliminate waste, streamline processes, and improve overall efficiency. This involves mapping out current processes, identifying bottlenecks, and systematically eliminating any steps that don't add value.
Risk
The primary risk here is potential disruption to production during the implementation phase. Employees may resist changes to their routine, fearing job loss or increased workload.
Implementation Challenges
Overcoming resistance to change requires strong leadership and clear communication. Continuous training and support are needed to help employees adapt to new processes. Additionally, constant monitoring is essential to ensure improvements are sustained over time.
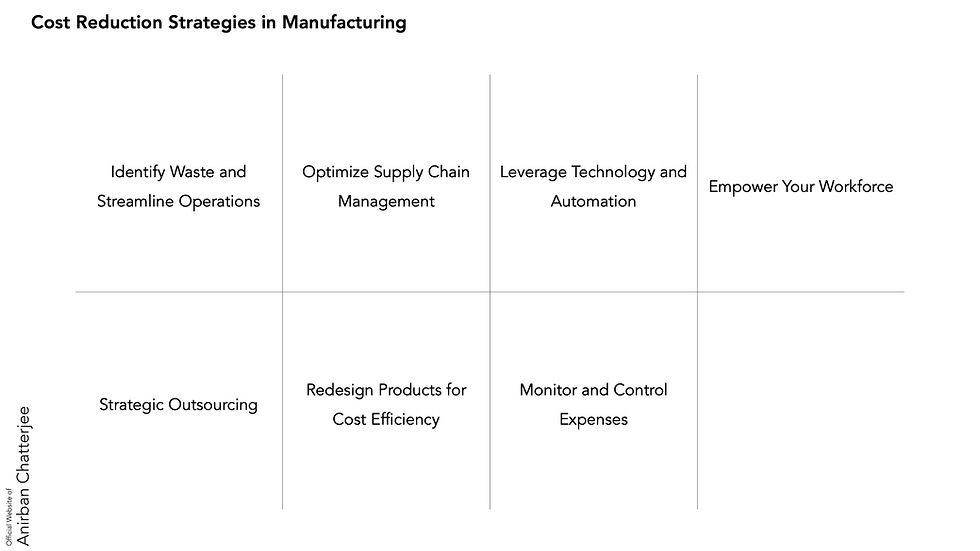
Optimize Supply Chain Management
Approach
Conduct a comprehensive supply chain review to identify inefficiencies and negotiate better terms with suppliers. Implementing a blockchain system can provide enhanced visibility and coordination across the supply chain, facilitating better decision-making.
Risk
Supply chain optimization can be risky due to potential disruptions, such as supplier delays or failures. Increased dependency on key suppliers can also pose a risk if they encounter problems.
Implementation Challenges
Integrating new systems with existing processes can be complex and time-consuming. Ensuring supplier compliance with new terms and processes requires careful management and ongoing communication. Organizational change management is critical to align all stakeholders with the new system.
Leverage Technology and Automation
Approach
Invest in automation and advanced technologies like IoT and AI to optimize production processes and reduce labor costs. Automation can handle repetitive tasks more efficiently, while IoT and AI can provide real-time data for predictive maintenance and process optimization.
Risk
High initial investment costs are a significant risk, as the return on investment may take time to materialize. Automation may also lead to job displacement, which can affect employee morale. Additionally, these technologies can introduce cybersecurity threats.
Implementation Challenges
Significant capital expenditure is required upfront, which may strain financial resources. Training employees to operate and maintain new technologies is crucial to ensure they are used effectively. Ensuring data security and integrating new systems with existing ones can also be challenging.

Empower Your Workforce
Approach
Foster a culture of continuous improvement by encouraging employees to suggest cost-saving ideas. Provide training and development opportunities to enhance their skills and productivity. Empowering employees can lead to innovative solutions and a more engaged workforce.
Risk
Initial resistance from employees is a common risk, as they may be sceptical about the changes or fear additional workload. Productivity might dip temporarily during training periods.
Implementation Challenges
Sustaining employee engagement over the long term requires ongoing motivation and recognition. Ensuring consistent training quality is essential for building the necessary skills. Aligning individual goals with organizational objectives can be complex but is crucial for success.
Strategic Outsourcing
Approach
Outsource non-core activities to specialized providers, allowing the company to focus on core competencies while benefiting from external partners' cost efficiencies and expertise. This includes logistics, IT services, or specific production processes.
Risk
Outsourcing comes with the risk of losing control over the quality and timeliness of the outsourced functions. There may also be security concerns, particularly with IT services.
Implementation Challenges
Selecting the right outsourcing partners is critical and requires thorough due diligence. Managing contracts and relationships with these partners demands ongoing effort and clear communication. Ensuring seamless integration with in-house processes can be complex and may require additional coordination.
Redesign Products for Cost Efficiency
Approach
Engage in value engineering to re-evaluate product designs, using alternative materials that are less expensive but maintain quality. Simplify the manufacturing process to reduce costs while ensuring the product meets customer expectations.
Risk
Changes in product design can impact quality and customer perception. There is a risk that the market may not accept the redesigned product if it deviates too much from the original.
Implementation Challenges
Balancing cost reduction with maintaining product quality is a delicate task. Coordinating with R&D and production teams to implement changes smoothly is essential. Managing changes in the supply chain, such as sourcing new materials, requires careful planning and execution.
Monitor and Control Expenses
Approach
Implement a robust expense monitoring system to track and control costs. Regularly review financial reports to identify trends and areas of concern. Set clear budgetary goals and ensure all departments are aligned with the overall cost-reduction strategy.
Risk
Overreliance on financial controls without addressing underlying inefficiencies can be counterproductive. If there is a lack of clear communication and coordination, potential misalignment between departments may occur.
Implementation Challenges
Ensuring accurate and timely data collection is crucial for effective expense monitoring. Fostering accountability across departments requires a strong organizational culture and leadership. Maintaining flexibility to adapt to changing circumstances while controlling expenses can be challenging but is necessary for long-term success.
Conclusion
Reducing costs in manufacturing is a continuous journey that requires strategic planning, careful implementation, and ongoing monitoring. By addressing risks and challenges head-on, manufacturers can achieve sustainable cost reductions while enhancing efficiency and maintaining competitiveness in the market.
The ultimate goal is creating a leaner, more agile, resilient manufacturing operation.